On April 9, 2025, Clone Robotics shared a striking video on their official social media platforms, showcasing their latest humanoid robot, Protoclone V1. The footage captured the android suspended from the ceiling, flexing its synthetic muscles and performing lifelike movements that left viewers both amazed and unsettled. With over 1,000 artificial muscles and a translucent design revealing its intricate internal structure, Protoclone V1 has been hailed as the most anatomically accurate humanoid robot ever created.
The announcement was accompanied by bold claims about Protoclone’s capabilities and its potential to revolutionize industries ranging from domestic labor to hazardous environments. While the robot remains tethered for stability during demonstrations, Clone Robotics promises that future iterations will achieve autonomous movement through advanced hydraulic systems. This milestone marks another leap forward for the Poland-based startup, which has rapidly gained recognition for its innovative approach to biomimetic robotics.
In this article, we’ll dive deep into Clone Robotics’ journey, the groundbreaking technology behind Protoclone, and what this development means for the future of humanoid robots.
Clone Robotics: A Visionary Startup in Biomimetic Robotics
Clone Robotics was founded in 2021 with a bold mission: to create humanoid robots that replicate human biomechanics with unprecedented fidelity. Unlike traditional robotics companies that focus on rigid electromechanical designs, Clone Robotics adopted a biomimetic approach inspired by evolutionary biology. Their philosophy centers on building robots that mimic human anatomy first and layering intelligence atop this physical foundation.
The company’s headquarters in Poland houses a team of biomechanical engineers, AI researchers, and materials scientists working together to push the boundaries of humanoid robotics. Led by CEO Dhanush Radhakrishnan, Clone Robotics has quickly become one of the most exciting names in the field. Radhakrishnan’s statement that “If you stab a Protoclone, it would bleed out—not because we want drama, but because water is its lifeblood” encapsulates their commitment to creating robots that function like living organisms.
The Technology Behind Protoclone
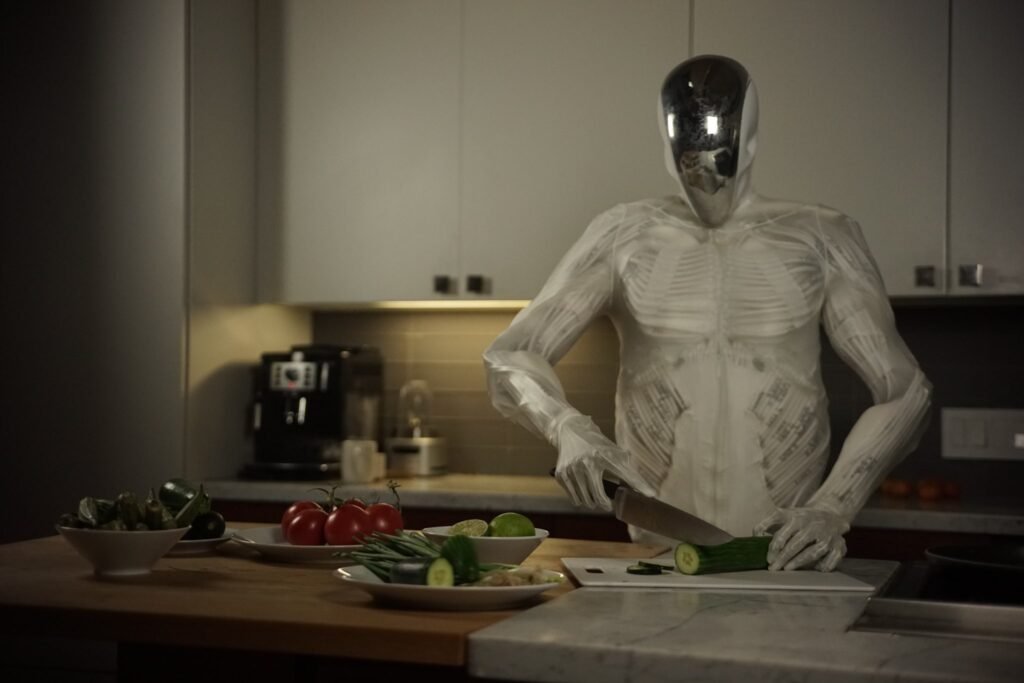
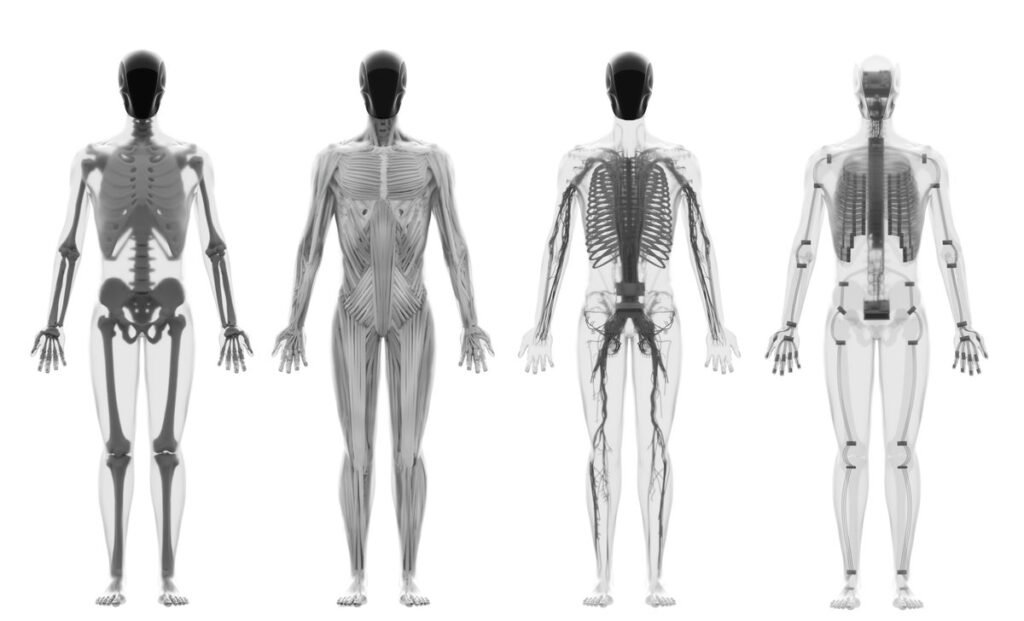
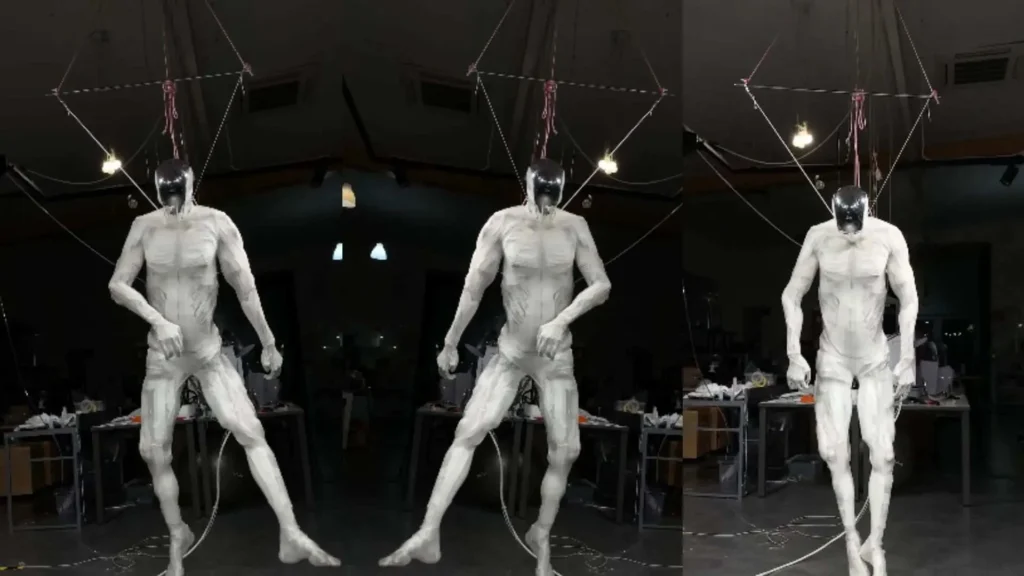
Protoclone V1 represents the culmination of years of research and development into biomimetic design. Its lifelike movements and anatomical accuracy are made possible by several key innovations:
1. Myofiber Artificial Muscles
At the heart of Protoclone’s design are Myofiber artificial muscles—synthetic actuators that mimic human skeletal muscles. These muscles are made from electroactive polymer sheets layered with microfluidic channels. Each muscle can contract by 30% in under 50 milliseconds when pressurized with fluid and generates 1 kilogram of force per 3 grams of material.
Unlike traditional robotic actuators that rely on rigid mechanisms, Myofibers provide flexibility and strength comparable to human muscles. They are connected to anatomically accurate polymer bones via synthetic tendons, enabling lifelike motion across more than 200 degrees of freedom.
2. Hydraulic Vascular Network
Protoclone’s movement is powered by a hydraulic system that mimics the circulatory system in humans. A high-efficiency pump circulates deionized water through elastomer tubes embedded throughout the robot’s body. This hydraulic fluid serves as both a power source for muscle contractions and a coolant to prevent overheating during operation.
Innovations in this system include:
- Aqua Jet Valves: Piezoelectric regulators that adjust fluid flow rates with millisecond precision.
- Pressure Gradients: Mimicking human blood pressure levels to ensure smooth muscle actuation.
- Closed-Loop Recycling: Recovering 98% of hydraulic fluid to minimize maintenance.
3. Sensor Integration
Protoclone is equipped with over 500 sensors that provide real-time feedback for precise control:
- Proprioception: Inertial measurement units (IMUs) track limb positioning.
- Tactile Feedback: Pressure sensors embedded in hands and feet detect forces ranging from 0.1 to 50 Newtons.
- Vision: A quad-camera array processes depth data at 60 Hz for spatial awareness.
These sensors allow Protoclone to perform delicate tasks requiring fine motor skills while maintaining balance and stability.
The AI Brain: Cybernet OS
Protoclone’s movements are controlled by Clone Robotics’ proprietary Cybernet OS running on NVIDIA Jetson Thor GPUs. This software integrates several advanced AI technologies:
- Visuomotor Transforms: Mapping visual input from cameras to muscle actuation in real time.
- Reinforcement Learning: Training the robot in simulated environments before physical trials.
- Ethical Constraints: Hard-coded safeguards prevent autonomous weaponization or harmful behaviors.
One of Protoclone’s most impressive features is its ability to learn tasks through observation. In a recent demonstration, a unit replicated a barista’s latte art after watching three examples—a milestone in imitation learning.
Development Timeline
Clone Robotics has made rapid progress since its inception, iterating through multiple prototypes before unveiling Protoclone V1:
Version | Year | Milestone |
---|---|---|
Alpha | 2022 | First Myofiber hand prototype catches a baseball |
Beta | 2023 | Torso prototype performs sit-ups |
V1 | 2024 | Full-body unit kicks soccer ball with lifelike motion |
V2 | 2025 | Suspension-free balancing (currently in development) |
Early prototypes required ceiling-mounted rigs for stability due to limitations in pneumatic actuators. However, Clone Robotics is transitioning to hydraulic systems capable of autonomous balance corrections using gyroscopic inertia wheels embedded in the pelvis—a design inspired by satellite stabilization mechanisms.
Applications Across Industries
Protoclone’s biomimetic design opens up possibilities for deployment across various sectors:
1. Domestic Labor
Clone Robotics envisions Protoclones performing household chores such as:
- Washing dishes
- Folding laundry
- Vacuuming carpets
- Preparing meals
Their lifelike dexterity allows them to handle delicate items without causing damage, making them ideal for tasks requiring precision.
2. Hazardous Environments
Protoclones are designed to operate safely in environments too dangerous for humans:
- Inspecting nuclear reactors
- Repairing live electrical lines
- Conducting deep-sea exploration
Their hydraulic systems are resistant to electromagnetic pulses and extreme temperatures, ensuring reliability under harsh conditions.
3. AI Research
Protoclones provide researchers with an anatomically accurate platform for studying embodied cognition—the relationship between physical form and intelligence. They also enable experiments in human-robot collaboration and emotional intelligence modeling.
Challenges and Controversies
Despite its groundbreaking design, Protoclone faces several challenges:
1. Technical Limitations
Current models require external support during demonstrations due to stability issues with pneumatic actuators. While hydraulic systems promise improved balance control, achieving autonomous movement remains an ongoing challenge.
2. The “Uncanny Valley” Effect
Protoclone’s lifelike movements have drawn mixed reactions from viewers. A study conducted by MIT found that:
- 62% of participants felt uneasy watching the robot blink asymmetrically.
- 41% reported anxiety upon hearing its hydraulic “breathing” sounds.
Clone Robotics argues that avoiding facial features minimizes discomfort associated with the uncanny valley phenomenon.
3. Ethical Concerns
Critics warn that hyper-realistic androids could be misused for:
- Industrial espionage
- Social engineering attacks
- Military applications
While Clone Robotics has implemented safeguards against weaponization, these concerns highlight the need for regulatory oversight as humanoid robots become more advanced.
Future Prospects
Clone Robotics plans to release Protoclone V1 in limited numbers later this year while continuing development on autonomous movement systems powered by hydraulics. Their long-term vision includes mass-producing affordable androids capable of transforming daily life and industrial processes worldwide.
Upcoming innovations include:
- Myofiber v2: Reinforced with carbon nanotubes for stronger contractions.
- Cerebral Hydraulics: Fluid-driven neuromorphic processors for advanced AI capabilities.
- Biodegradable Components: Reducing environmental impact through sustainable materials.
With competitors like Tesla’s Optimus and Boston Dynamics’ Atlas vying for dominance in humanoid robotics, Clone Robotics’ focus on biomimetic design sets it apart as a leader in this emerging field.
Conclusion
The April 9 post showcasing Protoclone V1 is more than just an impressive demonstration—it’s a glimpse into the future of humanoid robotics. Clone Robotics’ commitment to replicating human anatomy through cutting-edge technology has positioned them as pioneers in biomimetic design. While challenges remain, their work raises important questions about how robots will integrate into society—not just as tools but as partners capable of understanding and interacting with humans on an unprecedented level.
As CEO Dhanush Radhakrishnan aptly stated, “We’re not building better machines; we’re engineering better humans.” Whether this vision inspires or unnerves us, it undeniably pushes the boundaries of what robotics can achieve—and what it means to be human in an age of synthetic lifeforms.